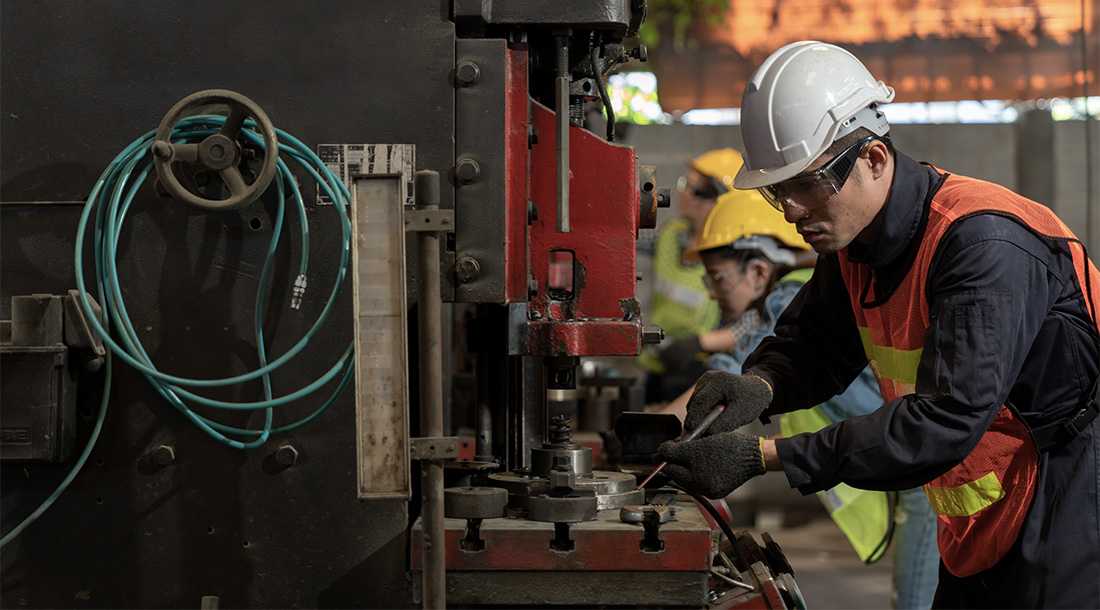
The Six Big Losses and How to Address Them
Overall Equipment Effectiveness (OEE) is one of the most important productivity metrics for manufacturers. Understanding how to increase OEE is critical for operating efficiently and maximizing productivity at your plant or facility. One of the best ways to improve your OEE is by targeting the Six Big Losses.
Let’s look at each of the Six Big Losses and what you can do to minimize them.
What are the Six Big Losses?
The Six Big Losses are used as a method for categorizing equipment-based losses. This helps manufacturers identify specific areas for improvement within their operations.
The Six Big Losses fit within the three factors that impact OEE: Availability, Performance, and Quality. Therefore, minimizing or eliminating the Six Big Losses will have a direct impact on your OEE.
The Six Big Losses are:
Unplanned Stops
Unplanned stops occur when equipment is scheduled for production but is not running due to an unplanned event, such as equipment failure or unscheduled maintenance.
Planned Stops
Planned stops occur when equipment is not running during normally scheduled production times due to a planned event. This includes changeovers, scheduled cleaning and maintenance, or inspections.
Small Stops
Small stops occur when equipment stops briefly — no longer than 10 minutes, but most often a minute or two. These stops are typically resolved by the operator; examples include material jams, sensor issues, or misfeeds. Though each individual stop is brief, small stops may happen frequently and chronically.
Slow Cycles
Slow cycles occur when equipment runs slower than the ideal cycle time, or the theoretical fastest cycle time possible under optimal circumstances. Common factors that lead to slow cycles include dirty equipment, poor lubrication, or operator inexperience.
Production Rejects
Production rejects are the defective parts produced during stable production. This includes scrapped parts and parts that can be reworked. Production rejects may happen due to factors such as operator error or incorrect equipment settings.
Startup Rejects
Like production rejects, startup rejects are defective parts, but only those produced from startup until stable production. This typically occurs during the start of production or after changeovers.
How to Address the Six Big Losses
The Six Big Losses can function as a compass for improving your OEE, so knowing how to minimize (and ideally eliminate) these losses within your operation is critical.
Automate Data Collection
When it comes to the Six Big Losses, accurate data is key. Some losses — such as small stops and slow cycles — can be difficult to measure, especially when done manually. Therefore, automating data collection is an important step for targeting the Six Big Losses.
Some platforms may offer specialized tools to help you measure and monitor the Six Big Losses, making it even easier to accurately assess your losses and identify the necessary steps to minimize them.
Take Preventative Steps
One of the best ways to reduce the Six Big Losses is implementing a preventative maintenance schedule and routine quality checks. Many of the Six Big Losses — such as unplanned stops or slow cycles — can be preemptively addressed by ensuring equipment is clean, properly calibrated, and generally well-maintained.
In addition to routine maintenance, take steps to ensure all employees know how to spot potential issues before they become a great source of loss.
Robust Training and Instructions
Operator error factors into several of the Six Big Losses. One of the ways to mitigate operator error — and reduce losses such as slow cycles or production rejects — is to set employees up for success with robust training and comprehensive reference material.
One modern solution is to provide employees with digital instructions that feature multimedia. Instructions that include images, video, or interactive elements can make it easier for all employees to understand the proper procedure and techniques required to operate equipment.
Identify and Focus on the Constraint
The constraint — or bottleneck — is the specific area of the manufacturing process that limits production. While it may be challenging, identifying the constraint is one of the most important steps in improving efficiency and OEE.
Identifying the constraint will help guide your decision on where to focus resources. Rather than attempting to address all of the Six Big Losses simultaneously, focusing your efforts on the constraint will make it easier to specifically address the most significant area of need, which will provide the quickest path to increased productivity.
Keep in mind that the constraint may move — it may be improved to the point that a new step becomes the constraint.
Need a Hand with the Six Big Losses?
Targeting the Six Big Losses is critical for improving productivity and your OEE. If you’re struggling to optimize your operations and increase productivity, you’re not alone — and Crescent Electric can help. With our robust line of time-saving products, industrial services, and industry expertise, we are uniquely positioned to help you increase the productivity and profitability of your business.
Learn more about the benefits are partnering with Crescent today — read more about our industrial services or contact us for more information!