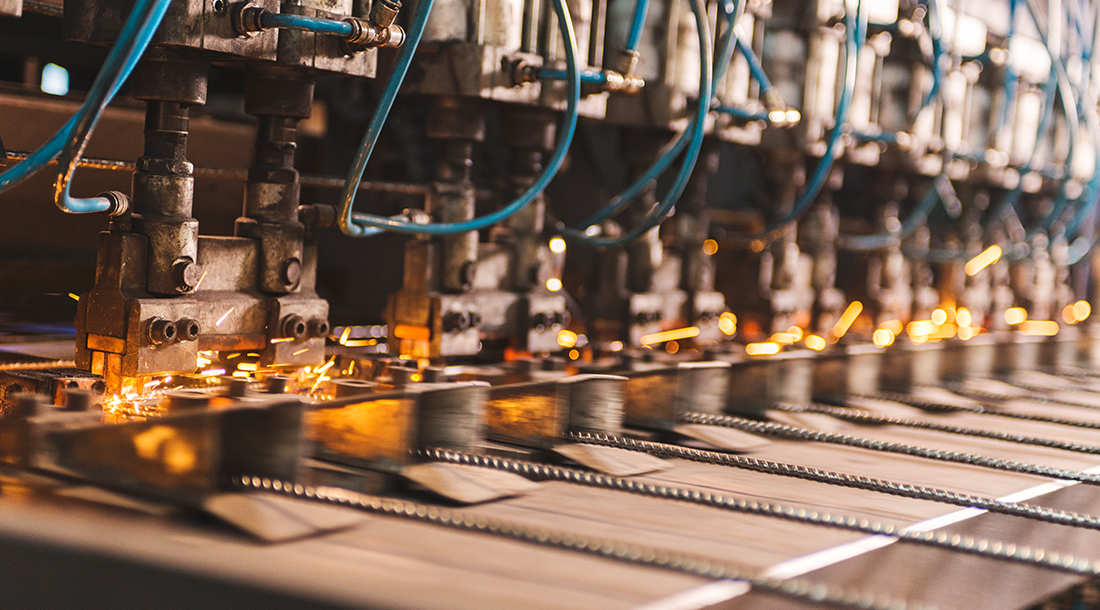
How to Improve Overall Equipment Effectiveness (OEE)
When it comes to improving industrial productivity, it’s important to consider not only how to do it, but also how to measure it. Identifying which KPIs to focus on will help guide your efforts and track your progress over time.
For industrial manufacturers, one essential metric to target is Overall Equipment Effectiveness (OEE). OEE is one of the best methods for assessing productivity levels and determining specific areas for improvement within your plant.
What is OEE?
Overall Equipment Effectiveness measures manufacturing productivity — or the percentage of manufacturing time that is productive. This allows manufacturers to evaluate the efficacy of a production process and determine where improvements can be made.
OEE considers three major components: availability, performance, and quality. Each of these factors is determined by its own calculation, and the three values are multiplied together to determine OEE. Knowing how to calculate OEE accurately is critical for assessing and improving productivity.
How to Improve OEE
Improving OEE is an important step in becoming more productive overall. Let’s look at a few actionable ways to improve OEE.
Automate Data Collection and Reporting
Given the importance of accurately calculating and monitoring OEE, automating data collection and reporting is a great way to minimize errors and ensure your data is always up to date. This alone won’t improve OEE, but it will allow you to diagnose areas for improvement quickly and easily.
With IIoT and various automation tools available, it’s easier than ever to make your data collection, analysis, and reporting more sophisticated and streamlined. This is a valuable step in improving your operations overall and, specifically, in improving OEE.
Display Real-Time OEE Data on the Floor
On the subject of data, displaying real-time OEE numbers will give you and operators insight into performance as its happening. Not only can this inform necessary adjustments, but studies also indicate it can boost employee engagement and productivity.
OEE dashboards are designed to visually depict real-time data such as machine performance or conditions. This can provide many benefits including more effective communication on the shop floor, reduced downtime, and reduced waste, all of which impact OEE.
Emphasize Preventative Maintenance
Equipment failure and downtime are major sources of lost productivity. Unplanned downtime can cost industrial manufacturers as much as $50 billion a year — so it’s no surprise that the most successful manufacturers emphasize minimizing downtime.
One of the best ways to achieve minimal downtime — and ultimately improve OEE — is to perform preventative maintenance. Following a routine maintenance schedule and training employees on how to spot potential machine issues are some of the best ways to ensure your machines keep running and your productivity stays high.
Eliminate the Six Big Losses
The Six Big Losses have major productivity implications. Focusing on these areas is critical for improving OEE. The Six Big Losses are:
- Unplanned Stops
- Planned Stops
- Small Stops
- Slow Cycle
- Production Rejects
- Startup Rejects
By gathering data on these six areas, you’ll have a good idea of which to prioritize and how to address them. Using this data as a framework, set specific goals and create actionable steps to minimize and, ideally, eliminate these losses.
Need Help Improving OEE?
Improving OEE is a constant process for industrial manufacturers, and consistently monitoring and assessing your OEE is essential for maximizing your productivity and profit.
If you’re looking for a partner in the process, Crescent Electric can help. In addition to a wide selection of industrial products from top manufacturers, Crescent can build solutions for your business — from everyday maintenance and supply items to sophisticated process efficiency improvements.
Visit our industrial services page to learn more, or contact us to get started!