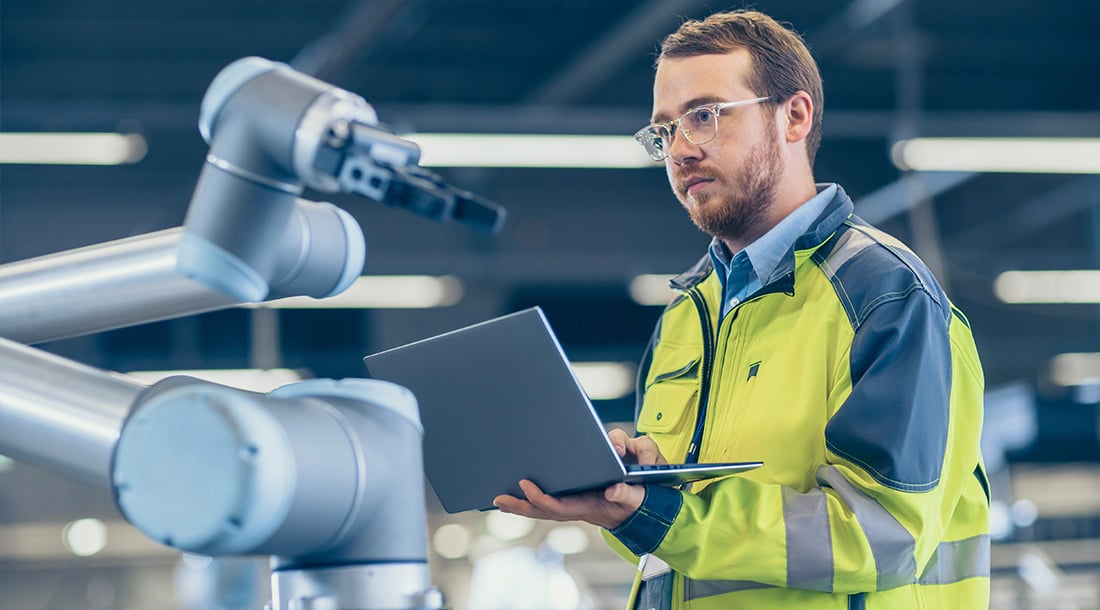
What Is Industry 5.0 and What Does It Mean for Manufacturers?
While the fourth industrial revolution, Industry 4.0, is the primary focus of many industrial manufacturers right now, technology moves quickly, and Industry 5.0 is already here.
For many manufacturers, Industry 5.0 represents “the future,” but some companies have already begun utilizing Industry 5.0 concepts. So while you continue to invest in and implement Industry 4.0 solutions, let’s take a closer look at Industry 5.0.
What Is Industry 5.0?
Industry 5.0 refers to the concept of humans working alongside the advanced, smart technologies introduced during Industry 4.0 to enhance the manufacturing process. Industry 5.0 is much more conceptual than Industry 4.0 — it seeks to leverage the creativity and skill of humans alongside the productivity and efficiency of smart machines and automation.
Therefore, it’s no surprise that Industry 5.0 followed Industry 4.0 so closely. For manufacturers, this means there isn’t another wave of tech coming, but rather a new way of thinking about how to optimally use Industry 4.0 technologies that are already being brought in.
Additionally, Industry 5.0 also includes the idea of shifting manufacturing from production-driven to value-driven. This means that Industry 5.0 practices emphasize human-centric, sustainable, and resilient manufacturing, all of which can contribute to added value to workers, customers, and society.
What Are Collaborative Robots (Cobots)?
One of the primary components of Industry 5.0 is the use of cobots in the manufacturing process. A cobot is a type of robot that works alongside a human. Unlike traditional industrial robotics which are programmed to complete specific tasks independently, cobots are versatile machines designed to work collaboratively with humans.
Cobots feature sensors and other technology that allow humans to safely work in their space. This means that workers can complete tasks like material handling or assembly more efficiently without sacrificing safety in the process. In fact, cobots can actually help reduce strain typically caused by tedious and repetitive tasks, which can lower the risk of workplace injuries.
Benefits of Industry 5.0
Industry 5.0 practices provide many of the same benefits that manufacturers can expect from transitioning their operations to Industry 4.0. However, Industry 5.0 also provides many additional benefits, most of which come from the shift to value-driven manufacturing. Let’s look at a few.
Better customization and personalization
Industry 5.0 practices are great for improving a manufacturer’s ability to serve customers with customized or personalized products that fit their needs. Manufacturers can achieve enhanced customization through strategies like leveraging the human-cobot relationship to utilizing advanced data to better understand customer needs.
Improved sustainability
Sustainability is a hot topic across most industries, and Industry 5.0 puts sustainability near the center of the production process. Industry 5.0 practices include reducing energy consumption and waste and minimizing the impact on natural resources, both of which contribute to more sustainable operations. This not only can have long-term benefits for manufacturers, but it will also help companies attract customers who prioritize sustainability in their purchasing decisions.
Enhanced resiliency
The COVID-19 pandemic exposed resiliency vulnerabilities in supply chains around the world, and Industry 5.0 specifically places emphasis on strengthening supply chains to avoid disruptions. This starts with big data analytics — technologies like artificial intelligence (AI) and machine learning can help manufacturers understand real-time data and gain insights that allow them to quickly make decisions.
Cybersecurity also plays a significant part in resilient manufacturing. As operations become more digitized through Industry 4.0 and 5.0, companies need to ensure their machines and technologies are protected against costly cyber-attacks.
Criticism of Industry 5.0
Some have criticized Industry 5.0 given its highly conceptual nature and how quickly it followed Industry 4.0. Paul Miller of the market research company Forrester says that Industry 4.0 initiatives should inherently be done with factors like sustainability and resiliency in mind. Instead of chasing Industry 5.0, Miller says that companies should focus on implementing Industry 4.0 properly and thoughtfully.
Industry 5.0 is a hot topic and one that will have lasting effects on the manufacturing industry. However, manufacturers should continue to prioritize Industry 4.0 as their true north — implementing these technologies will be paramount in gaining a competitive advantage and better serving customers. From there, keep Industry 5.0 on the radar as a way to optimize your Industry 4.0 strategy.
How Crescent Can Help
No matter where you are in modernizing your operations, Crescent can help — from our extensive product portfolio to industrial services specifically designed to help you modernize. Plus, our own Application Engineers can help you implement Industry 4.0 and 5.0 strategies to level up your business.
Visit our Modernization & Aging Assets page or contact us to get started!